4 Best Methods for Cutting Carbon Fiber by Hand
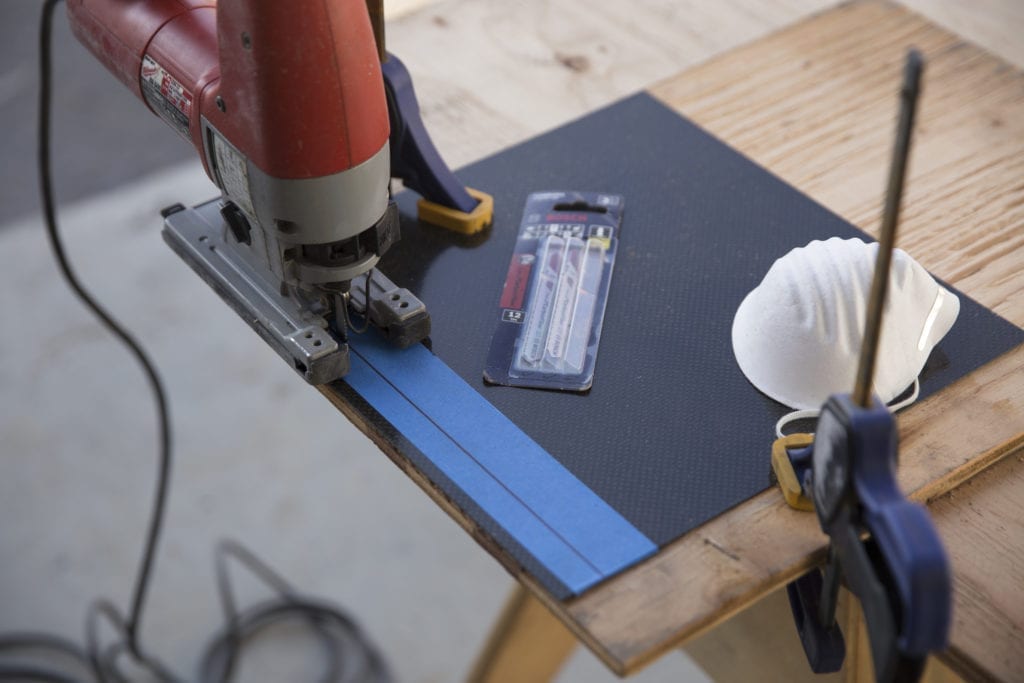
Cutting carbon fiber can be a difficult task without the right equipment. This post will help you cut your carbon fiber parts with low cost tools (some that you may already have in your garage), and do it without messing up the carbon fiber sheet you just bought.
Saftey First – Use Protection
Carbon fiber dust is an irritant and can cause itching if gets on your skin or difficulty breathing if you inhale it. Proper safety equipment will help prevent this. The following PPE is recommended.
- Long sleeves or a Tyvek paint suit
- Gloves, nitrile is ok, but leather or mechanic gloves are better when cutting or using power tools
- Dust mask or respirator
- Good ventilation, rigging a shop vac or using a downdraft table to collect the dust is better
- Eye protection, especially when using power tools
Preparation
Spending a little time up front for good preparation is an important part of producing quality parts, and it will save time and frustration later. These following tips will help.
- Tape Measure, remember to measure twice and cut once!
- Masking or painter’s tape, good for outlining where to cut, or allowing you to make more precise marks
- Marking tool, a metallic silver Sharpie works great directly on the carbon fiber, or you can use a pen or pencil on top of the masking tape
- Backing material helps get nice parts and reduce backside blow-out and splintering. You can use wood or rigid foam insulation to clamp your carbon fiber sheet to.
Method #1 - Hand Saws
Most of you already have a hacksaw and/or coping saw in the garage. A metal cutting blade on one of these saws will work well for cutting straight lines in carbon fiber. Even though the blade will dull quickly they are low cost and get the job done. You want to select a blade with a higher TPI (teeth per inch) this will give you a better cut. A thinner blade will help make sharper corners and get more detail. For interior features a hole can be pre-drilled that allows the blade to pass through the part on the inside. (See our other post on drilling carbon fiber.)
Method #2 - Rotary Tool
If you have a rotary cutting tool such as a Dremel, this is a great starting point for cutting carbon fiber. A standard abrasive metal cutting wheel works, but it will degrade quickly. If you are doing a lot of cutting you will be better off getting a diamond coated cutting wheel that is used for cutting tile. They are more expensive, but they will hold up much longer.
For cleaning up interior features or hand milling more complex shapes you can use the aluminum oxide grinding bit or a rotary sanding bit included in your Dremel took kit for the detail work.
Method #3 - Angle Grinder
A step up from the rotary cutting tool is an angle grinder. If you work a lot with metal or do welding, you are very familiar with what an angle grinder can do. It can make easy work of cutting straight lines in carbon fiber as well. A standard metal cutting abrasive wheel is the tool of choice for this type of cutting. As always, be careful, an angle grinder is a powerful tool and should be used with caution and the appropriate protective gear. A face shield would be a recommended upgrade over safety glasses.
Method #4 - Jig Saw
A jigsaw works well for cutting straight lines and getting into tight corners. A standard metal cutting blade will work OK but it will burn out after about 3-4 feet of cutting. Bosch makes a carbon fiber jigsaw blade that works incredibly well, you should be able to cut over 10 times more using one of these blades than a typical metal blade. You will want to use a backing material underneath the carbon fiber to get a cleaner cut. We like jig saws that you can attach a vacuum to, which helps control the dust.
Additional Resources
Easy Composites is a great resource for more information regarding composites safety and manufacturing techniques. Click here to see their video.
Good luck on your project and let us know if you have any other questions in the comments below.
If you have other tips or tricks that work well for you we would love to hear them.
I found the every best way to cut carbon fiber is to use a wet saw makes a nice clean cut ,and there is no dust.
nice answer. very clever.
Here in your list of hand saw blade which handsaw you will recommend for me
The success of a jigsaw tool depends on its blade. So you have presented this issue here in a very beautiful way.
Can you cut carbon fiber after you clear coat it or is it best to clear coat after cutting? I’m making a dash panel and it would be much easier to clear coat one big piece then cut to smaller pieces. I dont care if the edges are clear coated.
Hi Sean, I think it is best to clear coat after cutting because there is a good chance you could scratch the clear coat during cutting or edge clean up. You certainly could clear coat first, but then you would have to be very careful while cutting, even if you put a protective film over the surface.
Both clear coat and epoxy can be sanded and polished to remove scratches or to level low/high spots, assuming you have enough thickness of the clear to sand and polish down. If it’s easier to clear coat a sheet of carbon fiber, and cut out the piece parts, you can touch up the edges either by sanding (progressively) and polishing the abraded edges, and/or you can apply clear coat or epoxy to the perimeter edge and feather it in.
Would an Oscillating Multi-Tool work for cutting CF and would it be better than a dremel?
An Oscillating Multi-Tool would work, but you would need to use a blade designed for carbon, or an abrasive blade similar to the Dremel cutting disk. A blade designed for wood or metal would work for a short amount of time, and dull very quickly.
I use a diamond coated blade in my oscillating tool to cut and trim carbon fiber parts, and it’s my go-to tool for fast spot removal of material, and it often works great for linear trimming/cutting. What’s fabulous is, because the tool oscillates, it doesn’t spray carbon fiber dust everywhere, so it’s easy to suck the dust up with a vacuum as you work. It’s also somewhat easier to control than a rotary tool since there’s no rotational grab forces like with a spinning disc or shaft, though it has it’s own idiosyncrasies.
The dremel handles everything else, and I typically use a fiber or diamond cutoff wheel to make fast or deep linear cuts. Control can be tricky, as the cutting direction is perpendicular to the tool length, and the depth the wheel plunges into the material versus motor torque and cutting rate is controlled by the positioning and articulation of your hand and wrist, as you try to cut along a line. Then there’s the black roost of nasty carbon micro-fibers that sprays either towards, or away from you, depending on which direction your cutting from, making it tricky to contain/collect. I often set up a ghetto dust collection station by placing a large cardboard box on my workbench, with the side facing me open, and a live dust collection hose opening protruding through the far wall of the box. I try and shoot the black dust roost away from me and into the vacuum hose opening. I still wear a dust mask or respirator. Thin sheets can be cut with a paper shear. Waterjet is another option if you get to that scale.
The coolest way to cut carbon fiber, if you’ve done a wet layup, is to wait until the epoxy gels (the “green” stage), and then you can green trim the excess material with a razor or scissors. If you hit it at the right stage, it’s like a knife through hot butter. If you wait too long, then you have to turn it into fine dust to cut through it. Too soon, and it’s like a knife through honey and carbon fiber cloth (no fun at all). I often stop and open a vacuum bagged part early, because I’m impatient. If the part is still a little green, I grab a razor (and sometimes a bottle of acetone, to keep the blade moving) and zip off the excess carbon fiber, which brings feelings of great joy and satisfaction. Kind of like driving to work on a holiday, if your weekly commute normally is gridlock, and today there’s not a car on the road. Besides, you’re just stopping in briefly to pick up your bonus; call it green trim 🙂
I was considering using a standard band saw with a 1/4″ blade for some small radius cuts in some 2mm carbon fiber plate. It might ware on the blade a bit but I have only about 36″ of kerf to cut. What TPI would you suggest? The curve would be about 70 degrees over 4″.
Standard metal drill bits will work well on this material?
I was then figuring to finish the rough spots on the edge with a standard metal file. All this would be a small plate for a musical instrument where there would be threw fittings (1/4″ TS Jack) which may take a little strain from time to time. This would be superior over say, a 5mm piece of fiberglass, right?
Thanks for any help you can give.
Hi Timothy,
The bandsaw would cut through the fiber well. It likely wouldn’t get dull with that amount of cutting. Make sure you have a good method for collecting the dust and wear proper protection.
You might be better off using a sanding block with wet-dry paper over a file. A 2mm sheet should hold up to a 1/4″ TS Jack just fine.
Ryan,
Thanks for the tip. One of the things I had considered id using a piece of fiberglass in loo of the carbon fiber as I decided to use a plate for the jack (like a Fender strat output jack plate) I do like the appearance of the carbon fiber though. You guys don’t sell shorts do you?
Hi I was wondering if a palm router could work with a jig to copy a desired part? Obviously I would need to go slow but if this method would work what router bit would be needed, thanks
The dust generated could be quite significant. Make sure you have good dust collection and proper protection. We are going to be posting our recommended bits in a new blog post soon. A carbide fiberglass router would work well. Diamond-coating helps with durability but isn’t required for cutting. McMaster-Carr sells a couple that work well.
Anyone tried cutting with a Dremel motosaw?
The best way I have found to cut carbon is with an air tool and an abrasive disk. One thing not mentioned here is carbon dust is conducive and will eventually destroy an electrical tool. The wet saw is a great idea if you can stand the mess.
Would it be possible to use a Scroll Saw to cut .5mm C/F plates? And would I need to use a backing material attached to the C/F plate?
Thanks!
Lee
That would probably work, but I imagine that a standard blade would get dull very quickly. You would need to use a carbide blade. You will also want to make sure that you have good dust collection and wear the proper PPE.