Best Methods for Countersinking Holes in Carbon Fiber
Carbon fiber looks great, but it is tricky to work with. We have posted articles previously on how to drill holes and cut carbon fiber with readily available tools (here and here), and now in this post we will cover countersinking, because you don’t want ugly hardware heads ruining the look of your cool new carbon fiber part.
Safety First
If you haven’t already read our article on “The Good, Better and Best Ways to Drill Carbon Fiber,” take a minute to look at it now, especially the Safety and Preparation. Carbon fiber dust is an irritant and proper safety equipment should be used.
The Right Tools
High Speed Steel Countersink Bits
Countersinking is very similar to drilling when it comes to tool durability and finish. A standard HSS bit available in most hardware stores, or may even already be in your tool box, will work well when it is sharp, but will dull very quickly. You would be able to get about 10 holes before it goes bad and just starts burning the resin instead of cutting. A HSS bit will also leave frayed and splintered edges around the top of the countersunk hole.
Carbide Countersinks
If you want a tool that will last longer, carbide is the go to when working with carbon fiber. A carbide countersink will hold up for hundreds of holes without showing much wear. The carbide will work with hand tools the same way that a HSS bit will work, though it has a higher chance of grabbing your part and pulling itself into the carbon. The carbide may still casue some splintering of the top surface of the carbon, but not nearly as bad as the HSS. Putting masking tape over the area can help reduce it.
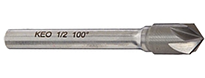
Carbide Rotary File
If you are looking for a perfect finish on the top side of your hole, a rotary file (also called burs) is the way to go. Both the double cut and the diamond pattern burs will work. These bits require higher rpm than a standard countersink, but will still work in a standard drill. McMaster-Carr has a wide selection of burs, we like the cone shaped ones pictured below.

Depth Control
For consistent depth on your countersinks, you can use what’s called a microstop. A microstop is commonly used for aircraft surfaces to make sure that all flat head screws are perfectly flush to minimize skin friction. Microstops require special bits called pilot cutters that will thread into the core of the microstop body. These bits are normally HSS but carbide ones can be found at some specialty stores. A word of caution with this tool, make sure the end of the microstop, and the surface of your part are clean, otherwise it can scratch your carbon fiber. Putting down a piece of masking tape over the section you want to countersink can help prevent this.
Take-Aways
- More flutes are better
- Higher speeds (RPM) give a better finish
- Solid carbide bits will hold up for hundreds of holes
- Rotary files will work well
Good luck on your project and let us know if you have any other questions in the comments below.
If you have other tips or tricks that work well for you we would love to hear them.
Way cool! Some extremely valid points! I appreciate you writing this post and the
rest of the website is also very good.
Hi there, just wanted to tell you, I liked this article.
It was practical. Keep on posting!
Great post