The Good, Better and Best Ways to Drill Carbon Fiber
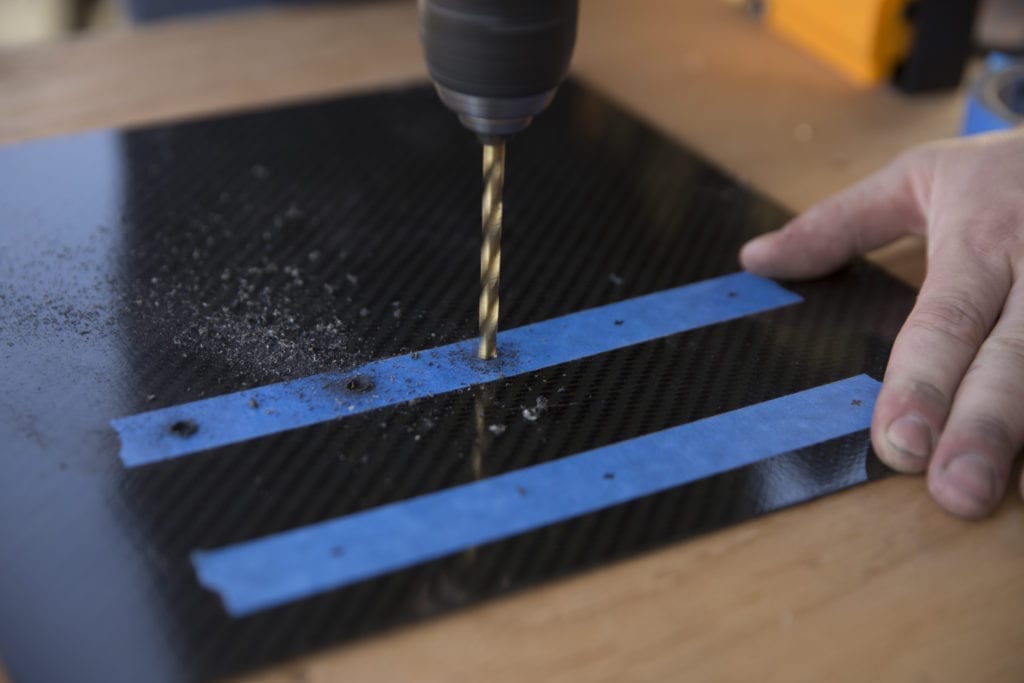
If you don't have the right tools and knowledge, drilling carbon fiber is a difficult task that will results in bad parts and ruined tools. In this post we will go over the good, better and best ways to drill carbon fiber and not ruin your parts or tools.
Safety First - Use Protection
Carbon fiber dust is an irritant and can cause major itching if gets on your skin or difficulty breathing if you inhale it. Proper safety equipment will help prevent this. The following PPE is recommended.
- Long sleeves or a Tyvek paint suit
- Gloves – nitrile is ok, but leather or mechanic gloves are better when cutting or using power tools
- Dust mask or respirator
- Good ventilation, rigging a shop vac or using a downdraft table to collect the dust is better
- Eye protection, especially when using power tools
Preparation
Spending a little time up front for good preparation is an important part of producing quality parts, and it will save time and frustration later. These following tips will help.
- Tape Measure, remember to measure twice and cut once!
- Masking or painter’s tape, good for outlining where to cut, or allowing you to make more precise marks
- Marking tool, a metallic silver Sharpie works great directly on the carbon fiber, or you can use a pen or pencil on top of the masking tape
- Backing material helps get nice parts and reduce backside blow-out and splintering. You can use wood or rigid foam insulation to clamp your carbon fiber sheet to.

The "Good" Way
Most of you already have an electric drill laying around, this is the simplest way to make holes in carbon fiber. You also probably have a set of high-speed steel (HSS) bits, these will work OK if they are sharp but they will dull quickly. A brand new bit will hold up for 5-10 holes before it is completely dull and will only serve to heat up and burn the resin. Drills that have a speed selector for higher RPM, like the DeWalt electric drill below are a good place to start.
The "Better" Way
If you are planning to drill more than 5-10 holes and don’t want to keep buying more HSS drill bits, there is a better option for great drill bits designed for durability and everyday use. These drill bits have tips that are coated with carbide or diamond which makes them harder and longer lasting than normal steel bits. Carbide tipped bits are reasonably priced and can be found at many places such as McMaster-Carr, which is a great resource for tools and hardware.

The "Best" Way
The best bits for drilling carbon fiber are solid carbide or diamond. These bits are very brittle though and should only be used in a rigid setup like a drill press or mill. If you try to use these with a hand drill, even if you use drill bushings, they can easily shatter. These bits are made to run at very high rpm (3000-5000rpm) and basically just turn the carbon into dust (make sure you are using protection!). Sometimes called brad-point drill bits, they cut fibers without fraying or delaminating the material and they eliminate splintering on both sides of the hole. These bits are incredibly durable and can withstand hundreds of holes if used properly.
Additional Tips
Putting masking tape over the area you want to drill allows accurate placement of the hole and helps reduce fraying of top surface material.
Running the drill at high RPMs (3,000-5,000) and a slow feed-rate, or low pressure, will reduce the possibility of delamination and splintering.
Good luck on your project and let us know if you have any other questions in the comments below.
If you have other tips or tricks that work well for you we would love to hear them.
Really helpful piece, but wait! This means that Mark Watney couldn’t really drill 720 holes through the top of a Carbon Fiber Mars Rover roof with a single geological drill bit!
Nice & Very helpfull to me .. It increase my knowdge…
Thanks Sir…
He could if he used a solid carbide bit!
That is informative article for me.
I added your web-site into my bookmarks!
🙂 Looking forward for new updates!
Best regards,
Robert
I’m not sure where you are getting your information, but great
topic. I needs to spend some time learning more or understanding more.
Thanks for fantastic information I was looking for
this info for my mission.
Appreciate this post. Will try it out.
Having read this I believed it was very informative.
I appreciate you spending some time and effort to put this short article together.
I once again find myself spending a significant amount of
time both reading and commenting. But so what, it was still worthwhile!
Brought to you by Dewalt
Thanks for the comment. We are in no way sponsored or affiliated with Dewalt. We like their tools and find that they offer good equipment at many different price points with a good warranty. We also use some Makita and Black & Decker products, but found Dewalt to offer a little more for the money.
Hi, I need to drill two 12mm holes in a Lizard Skins Large Frame Protector Carbon Leather patch. Is a carbide tipped bit going to be OK for this, do you know? The patch thickness is 1.4mm.
Hi Edward, if you only need two holes, you should be ok with a standard high speed steel (HSS) drill bit. I suggest placing the Carbon Leather patch on s scrap piece of wood when drilling the holes. Good luck!
Thanks For Sharing
Drilling through a carbon fiber hood wont cause it t crack/shatter correct? As long as the right bits are used.
Matt, that is correct, it will not crack or shatter. You can use normal high speed steel bits and they will work fine for 5-10 holes before it will get dull. The tighter weaves, like plain and twill will work better and look cleaner than the checker weave since the weave is spread out more, the fiber can start to pull up along the edge of the cut, especially on the back side of the cut.
Great information
Carbide Tip bits tend to burn up pretty quickly. The coating is heat sensitive and after 2-3 holes through 1/2″ panel will essentially make it an HSS bit for three times the price.
Hi Joe, What bits do you recommend for carbon? The carbide tip bits we reference above for hand drilling have a carbide insert that is more durable than just a coating. In our experience, coatings do wear off very quickly on carbon.
Why not masonry bits? They’re carbide, right? Is there an issue with how they’re fluted?
Also, this is great for drilling through flat sheets but what about making smooth cuts through a thick block of carbon? Say, if someone were using it as a pen blank?
The material is carbide, but it isn’t as sharp as the bits used for cutting through the carbon and the tip geometry is a bit different. Typically masonry bits are designed to be used with a hammer drill, which would likely delaminate your fibers.
yeah great information article. but if you want to look a best hammer drills buying guide. https://abbottcart.com/10-best-rotary-hammer-drills-reviews-buyer-guides/
Should you coat the raw carbon with epoxy after drilling?
It isn’t required if you can keep the hole free of burs or fiber pull up. Sanding or filing with water will achieve a similar effect.
Awesome!👍
I would to bore out the tube stem hole on my carbon fiber bicycle rims.
Can you foresee any issue w doing so?
It is difficult to say without seeing the rim. You should make sure that the location of the hole isn’t in a structural area. You will also want to be careful not to pull up fibers or clean out any fibers that do get pulled up.
I’m new to drilling stacked CF and i noticed that every manufacturer use different point geometry and step configurations to drill. Especially with power feed drills. The Aerospace Industry, which usually consist of holes under .266 seems to be all over the place with point angles. Stack material CF to Aluminum seems to be most common but I have applications CF to Titanium, which is rarely more that 1/2″ thick total. Is there a magical formula that is used for CF stack panels?
Any difference using a reamer or a drill to finish a hole
R finishing reamers better at making a clean hole wood it b Berger to make the hole larger and then put a coat of epoxy to add a few thousands back
Generally the reamer will get tighter tolerances and have less wear over a large number of holes. You certainly could add some epoxy back in, but I don’t think it would be worth the added time. The reamer should leave the hole clean. Depending on the material you’re cutting, you may need to add a chamfer to the top and bottom of the hole to ensure fibers don’t get pulled up.
I just want to attach a pickup to a carbon fiber guitar (2 holes). If I drill a pilot hole, will the screws hold?
Hi Great Article, Thank you. I’ll be drilling then screwing stainless bolts into a carbon fiber mast. I was going to put TefGel on the bolts Is that what you recommend?
Thanks,